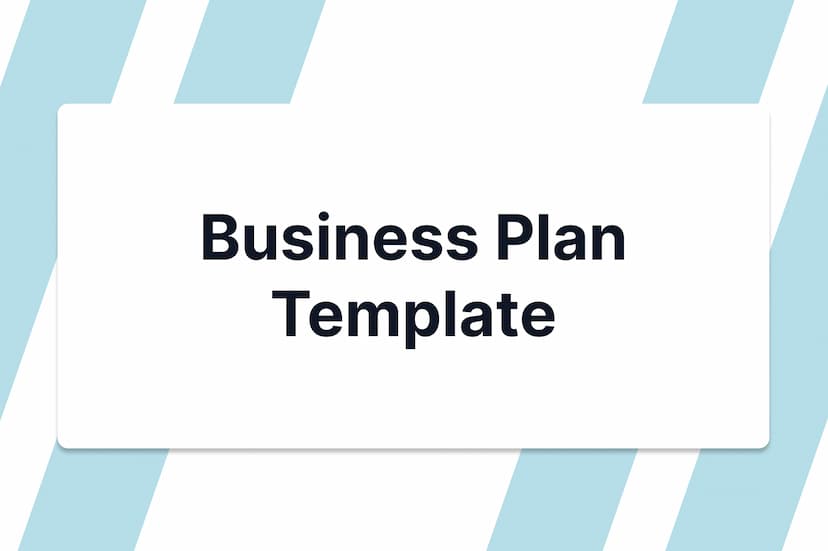
A Standard Operating Procedure (SOP) is a written, step-by-step instruction that describes how to perform a specific task or process within an organization. It serves as an essential reference for employees, detailing expectations for consistent and efficient task execution. SOPs are vital for maintaining quality, safety, and compliance in operations.
SOPs establish consistency in work processes, ensuring that tasks are completed uniformly, regardless of who performs them. They minimize risks, reduce error rates, and promote high standards by setting clear instructions for all involved. SOPs also play a critical role in maintaining compliance with industry standards or legal regulations, making them essential for safety and quality in industries like healthcare, manufacturing, and food services. For employees, they provide a clear understanding of roles, responsibilities, and expectations, helping to streamline onboarding and ongoing training.
SOPs are necessary when there’s a need for uniformity and compliance in task execution. They are crucial in industries with strict regulatory requirements (e.g., healthcare, pharmaceuticals, manufacturing), where the consequences of errors can be severe. SOPs are beneficial whenever a task is complex, frequently performed, or critical to safety or quality. They’re also valuable during transitions, such as when new employees join or teams restructure, providing continuity and clarity.
Employees at all levels refer to SOPs for guidance. Managers and supervisors use them to ensure tasks are completed according to established standards, while new hires rely on them during training. Quality control teams and auditors often review SOPs to verify compliance with standards and regulations.
Implementing an SOP effectively requires clear documentation, regular updates, and accessible distribution. Training sessions can reinforce adherence, while periodic reviews ensure procedures remain relevant and aligned with evolving business needs. Employee feedback can also be invaluable in refining SOPs to make them more practical and user-friendly.
SOPs should be stored in an easily accessible location, either digitally (e.g., company intranet, document management systems) or physically, to ensure employees can quickly reference them when needed.
State the objective of the SOP. Explain why this procedure exists and what it aims to achieve.
Define the applicability and limits of the SOP. Specify who it applies to, such as departments, roles, or processes, and any exclusions.
List and define any terms, abbreviations, or acronyms used in the SOP to ensure clarity.
Detail the roles and responsibilities of personnel involved in the procedure.
Provide a step-by-step guide to perform the procedure. Use clear and concise language.
Include diagrams, flowcharts, or images if they aid understanding.
Highlight any safety precautions, personal protective equipment (PPE) requirements, or regulatory compliance considerations.
List any documents, manuals, regulations, or other SOPs referenced in this procedure.
Record changes made to the SOP over time.
Version | Date | Description of Change | Author |
---|---|---|---|
1.0 | MM/DD/YYYY | Initial release | [Name and Title] |
1.1 | MM/DD/YYYY | [Describe what was updated] | [Name and Title] |
1.2 | MM/DD/YYYY | [Describe what was updated] | [Name and Title] |
Include any additional information that supports the SOP, such as forms, checklists, or detailed diagrams.
[Content]
[Content]
This template is designed to help you create comprehensive Standard Operating Procedures. Tailor each section to fit the specific needs and context of your organization.